End Covers - 2
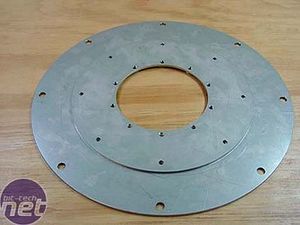
Once lined up...
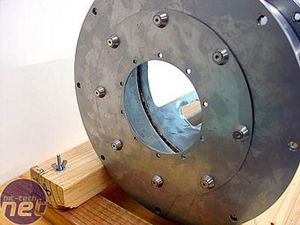
...the inside ring is secured using short M5 countersunk socket-head screws and Armor Rings.
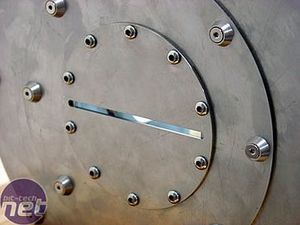
The cover is secured to the flange of the end section using the threaded tube/Armor Ring method that joins the rest of the case. The centre disc is simply screwed on using short M6 screws. Where will the eject button for the DVD go, I hear you ask? It will later be relocated to another part of the case.
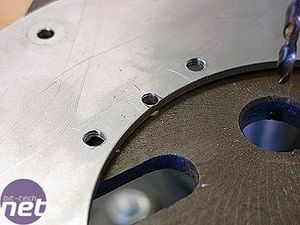
Once attached, the cover fits in well with the rest of the case and the protruding fasteners give it a heavy, industrial feel. There was one last task - cut-outs in the inside ring to accommodate the ends of the DVD slot. I started by marking and drilling the inner ring.
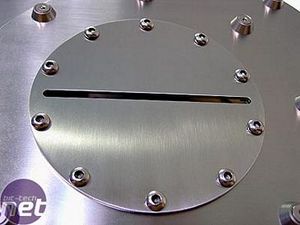
The hole was then widened with a larger drill bit and filed out. Once on, the slot is completely clear. The final polish with a flap-wheel took the sharp edges off the slot, but I will still be running a few tests once the mod is finished, by using some old discs to check for scratching and smoothing off any problem areas.
The Intake End
The plan for the intake end called for a bit more work...
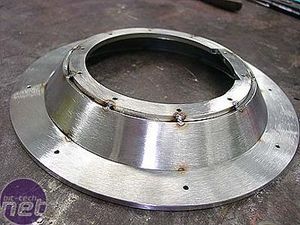
I started by getting 3 pieces of stainless laser-cut and then rolling and welding it into a 'dish' shape. The holes match those of the flat end cover pieces. The sloping part of the dish was rolled from a piece of steel cut in a specific way to mean that, when rolled, it would join up in a funnel shape (it was an open 'C' shape when flat). Time was critically short as this piece was made at the same time as the main cylinder and the timer box, so I didn't get many opportunities to take pics, but it was a fairly straightforward process - rolling and welding.
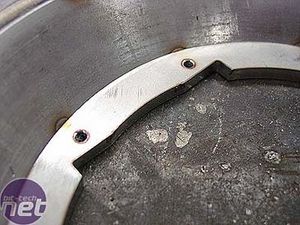
The pieces were tacked together first with small welds, to make sure everything lined up properly. I was a bit annoyed as the parts had come back from the laser cutters with a big section missing from the smaller flange (I suspect they re-used a scrap piece of steel to cut it from, and the cuts had ended up overlapping an existing hole). Not only that, but they'd cut it from 5mm stainless, not 3mm! OK, so it'll look pretty hardcore, but rolling 5mm stainless isn't much fun. A piece of steel was cut and shaped to fit in the hole, then welded in place and the joins ground down. The joins were then welded completely around the circumference and a few hours spent grinding and cleaning the piece up.
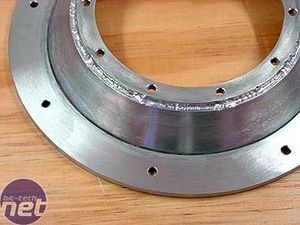
The finished 'dish'. You can't even tell the missing section existed. Time to cover that hole up...
Want to comment? Please log in.